Best Practices for Maintaining Industrial Vacuum Systems
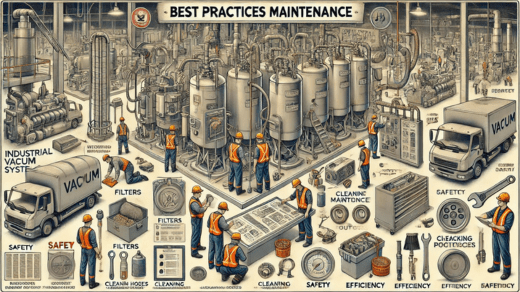
Conduct regular inspections, clean filters, and lubricate components to maintain industrial vacuum systems effectively. Follow manufacturer guidelines for maintenance schedules and use appropriate tools and equipment. Ensure proper operator training and prioritize safety protocols. Proactive maintenance enhances system performance, extends lifespan, and minimizes downtime.
Introduction to Industrial Vacuum Systems
Industrial vacuum systems are indispensable in numerous industries, including manufacturing, pharmaceuticals, and food processing. These systems are designed to handle rigorous cleaning, material handling, and environmental control tasks. Yet, the efficiency and longevity of these robust machines largely depend on routine maintenance. Whether using them for general applications or specialized functions like hydro excavation vacuum, the importance of upkeep cannot be overstated. It’s not just about keeping the machines operational; it’s about optimizing their performance and extending their useful life.
Why Regular Maintenance is Crucial
Failure to properly maintain industrial vacuum systems can result in numerous issues, ranging from reduced performance to total system failures. The repercussions of neglect can be particularly severe, leading to costly repairs and replacements. According to IndustryWeek, regular maintenance can drastically reduce the likelihood of unexpected downtimes and significantly extend the lifespan of the equipment. Properly maintained systems operate more efficiently, consume less energy, and deliver better results.
Basic Maintenance Steps
Regular maintenance tasks mainly fall into a few basic categories. By sticking to these simple yet essential practices, you can avoid the most common issues:
- Inspection: Conduct regular inspections to spot any signs of wear and tear. Components like hoses, filters, and seals should be scrutinized closely, as they are prone to degradation over time.
- Cleaning: Filters and hoses should be cleaned frequently to prevent clogs. A clogged filter can lead to system inefficiency and even damage if left unattended.
- Lubrication: Moving parts must be well-lubricated to minimize friction and avoid overheating. Proper lubrication helps in reducing the wear and tear on the system’s moving components.
- Monitoring: Monitor the system’s performance metrics, such as suction power and energy consumption. Any deviations from the norm can be an early indicator of potential issues.
Advanced Maintenance Tasks
While essential maintenance is crucial, some tasks require higher expertise and should be undertaken periodically for optimal performance.
Electrical Connections: Check and tighten all electrical connections to ensure they are secure. Loose connections can lead to a fluctuating power supply and may cause severe operational issues.
Sensor Calibration: Periodically calibrate sensors to ensure accurate readings. Incorrect sensor data can lead to improper system operation and can be a potential safety hazard.
Part Replacement: Replace worn-out parts such as gaskets, seals, and bearings. These components are critical to the vacuum system’s functionality, and their failure can cause extensive damage to other parts of the system.
It is often advisable to have these tasks performed by qualified technicians. They have the specialized skills and tools to carry out these advanced maintenance activities effectively. For individuals who want to learn more about maintenance nuances, the Maintenance Community offers excellent resources and guidelines for advanced maintenance chores.
Common Issues and How to Solve Them
Despite your best efforts, issues may still arise. Common problems include clogging, loss of suction, and unusual noises, all of which can severely affect the system’s performance. Resolving these problems early on is essential to preserving system performance.
Clogging: This is often caused by debris getting stuck in filters or hoses. Regular cleaning can prevent this problem, but a more intensive cleaning or component replacement may sometimes be necessary.
Loss of Suction: A failed motor, a leak in the system, or a clogged filter can all cause a drop in suction power. An in-depth examination of the system is necessary to determine the root cause.
Unusual Noises: Strange noises often indicate that something is not functioning correctly. It can result from worn-out bearings, loose parts, or mechanical problems. Immediate attention to this issue can prevent further damage.
Extending the Life and Efficiency of Your Equipment
Proper maintenance extends a system’s lifespan, improves efficiency, and keeps it operating. Consistent maintenance practices ensure that all aspects of the system are regularly checked, identifying and addressing potential issues before they escalate. This ensures continuous operation and preserves the machine’s optimal functionality.
Adopting a comprehensive maintenance schedule is an effective way to ensure systematic checks and services. Regularly scheduled maintenance can predict parts needing replacement soon, preventing untimely breakdowns. This timetable should include basic and advanced maintenance tasks, making it a holistic approach to system care.
Conclusion
Maintaining industrial vacuum systems is vital for ensuring their long-term efficacy and durability. By adhering to best practices for basic and advanced maintenance, businesses can avoid costly repairs and extend the lifespan of their vacuum systems. This proactive approach secures a continuous return on investment and enhances operational efficiency. For more detailed information, refer to resources like IndustryWeek and the Maintenance Community, which offer extensive insights into effective maintenance strategies.