Can PA material be used for plastic CNC machining?
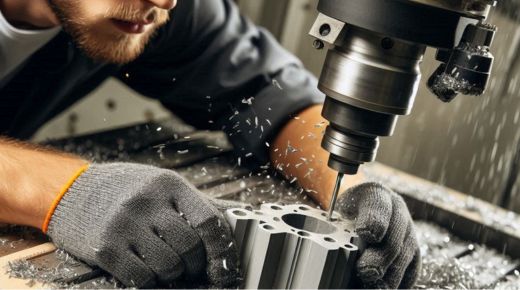
Polyamide (PA), commonly known as nylon, is a plastic widely used in engineering applications. PA has various types, such as PA 6 and PA 6/66, which are very suitable for plastic CNC machining. Here are some advantages of using PA for CNC machining:
Good mechanical properties: PA has a high melting temperature, which makes it an ideal substitute for metals that need to be used in high temperature environments.
Processing tips: Since PA has lower impact strength than other plastics, it is necessary to pay attention to controlling tool speed and cooling during CNC machining to avoid cracks, deformation or burrs.
Minimize clamping force: During CNC machining, minimizing clamping force can reduce internal stress and prevent part damage.
Choose the right tool: Using tools suitable for plastic machining can reduce tool winding and improve machining quality.
In summary, PA is a material that can be processed by CNC, but special attention needs to be paid to various details during the machining process to ensure the quality of the final product.
The difference between processing engineering plastics with an engineering plastics processing center and injection molding plastics:
1. CNC machining starts with a piece of material, accurately removes a layer of material at a time, and after removing the material multiple times, a set shape is obtained. This process allows the use of many different materials with almost no restrictions. In addition, it is computer-controlled, so very precise tolerances can be achieved.
2. Injection-molded engineering plastics are liquid plastics injected into the mold, generally by high-pressure liquid plastics pressed into the mold. The corresponding parts can be obtained after cooling. This method has high mold costs, and the plastic parts have burrs and low precision.
3. Speed: If the number of parts is small, CNC machining is the fastest. If you need 10 parts in 2 weeks, CNC machining may be the only solution (3D printing is also an option). If you need 50,000 parts in 4 months, injection molding is the best choice. Injection molding requires time to build the mold and ensure that the parts are within tolerance. This can take weeks or months. Once this is done, using the mold to make the part is a very fast process.
4. Price: Which one is cheaper depends on the quantity. If you are producing hundreds of parts, CNC will be cheaper. When the production quantity reaches a certain amount, injection molding will be cheaper. In fact, no matter how many pieces are produced, the cost per piece, injection molding is cheaper than CNC machining. However, injection molding needs to share the cost of the mold.
5. Materials:
CNC machining supports more materials, especially some high-performance plastics or specific plastics, but is not good at processing soft materials.
Injection molding has relatively fewer materials, but there are some materials that can be injection molded now, which cannot be used for CNC machining. In addition, injection molding can process soft materials.
6. Tolerance/Surface Finish:
CNC machining is more advantageous in this regard. For most materials, tighter tolerances can be maintained and better surface finish can be obtained. One of the advantages of injection molding is batch-to-batch repeatability. The mold can withstand millions of parts with minimal wear. This allows parts to be almost identical from one batch to the next.
7. Design:
CNC machining has fewer restrictions and can support more designs. In addition, if the parts produced have a fast update cycle, CNC machining is also more suitable.
Be-Cu provides the highest standard of cnc machining and metal spinning china service for all your needs. Contact us today to know more about what we offer!
- Sales: Bella
- Web: metal-spun.com
- Phone: +86 151 1280 7161
- Email: [email protected]
- Affiliated: Be-cu Prototype
- Address: Dongguan,China