The Right Time to Invest in an Alabama Robotics Engineering Company for Automated Flash Removal in Metal Casting
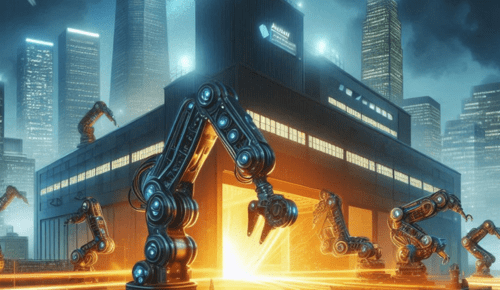
In metal casting, precision matters. When flash removal is inconsistent, product quality suffers, leading to higher costs and dissatisfied customers. As demand for efficiency grows, many manufacturers are turning to an Alabama robotics engineering company to automate flash removal and ensure consistent results. Here’s why now is the perfect time to make the switch.
Rising Defect Rates from Inconsistent Manual Flash Removal That Compromise Product Quality
Manual flash removal has long been a standard practice in metal casting, but it’s also one of the biggest sources of defects. Human error, fatigue, and inconsistent techniques create uneven surfaces, weak points, and quality issues that affect the final product. Even the most skilled workers struggle to maintain precision over long shifts, leading to variability that impacts structural integrity. When defects make it past quality control, they result in costly returns, warranty claims, and potential damage to a company’s reputation.
Automating flash removal eliminates these risks by ensuring every part is trimmed with precision. A robotics engineering company in Alabama can integrate advanced robotic systems that consistently remove flash without damaging the casting itself. With a high level of repeatability, these systems improve product reliability and significantly reduce the number of defective parts, saving manufacturers time and money.
Variability in Flash Removal Quality That Leads to Customer Complaints and Rework Expenses
A single bad batch can lead to a flood of customer complaints. When manual workers remove flash by hand, the level of detail and accuracy varies from part to part. This inconsistency leads to rough edges, uneven surfaces, and missed spots that result in rework, scrapped materials, and lost productivity. Over time, these issues add up, increasing operational costs and damaging relationships with clients who expect uniform, high-quality parts.
Robotic automation ensures every casting meets the same exacting standards. With programmed precision, an Alabama robotics engineering company can implement systems that eliminate variation, delivering smooth, defect-free components every time. This consistency leads to fewer complaints, reduced waste, and a more reliable production process that meets customer expectations without the need for costly rework.
Excess Material Waste That Could Be Minimized with Precision Robotic Trimming
Material waste is one of the hidden costs of manual flash removal. Traditional methods often result in excessive grinding, over-trimming, or discarded parts that fail inspection. Workers using hand tools may unintentionally remove too much material or leave excess flash behind, requiring additional processing. These inefficiencies not only drive up material costs but also increase production time and overall expenses.
Robotic flash removal optimizes material usage by trimming only what’s necessary. The advanced vision systems and programmed cutting paths used in automated solutions ensure maximum precision, reducing scrap and unnecessary waste. Partnering with a robotics engineering company in Alabama allows manufacturers to minimize material loss while improving yield, resulting in a more cost-effective and sustainable operation.
Limited Scalability in Operations Due to the Physical Limitations of Manual Processing
Growing a manufacturing operation requires efficiency, but manual processing has limits. Workers can only remove flash at a certain speed before fatigue sets in, and hiring more employees isn’t always feasible due to labor shortages or rising wages. As demand increases, companies relying solely on manual labor struggle to scale up production without compromising quality or overloading their workforce.
Robotic automation provides a solution that grows with production needs. A well-integrated system from an Alabama robotics engineering company can operate around the clock, delivering the same high level of accuracy without the constraints of human fatigue. This scalability allows manufacturers to meet higher demand, reduce lead times, and improve overall productivity without needing to constantly expand their labor force.
Compliance Issues with Industry Standards That Require Consistent Surface Finishing
Inconsistent flash removal isn’t just a quality issue—it’s a compliance risk. Many industries, including automotive, aerospace, and medical manufacturing, have strict surface finishing standards that products must meet before reaching the market. Variability in manual processing increases the risk of non-compliance, leading to rejected shipments, fines, and regulatory setbacks.
Automated flash removal ensures every part meets the required specifications. Robotics solutions provide controlled precision that aligns with industry standards, eliminating the uncertainty of manual methods. By working with a robotics engineering company in Alabama, manufacturers can maintain compliance with regulations while improving overall efficiency, ensuring their products meet the highest quality standards without the risk of inconsistencies.